How our glasses are made
Every frame's journey begins in-house in our design studio in Amsterdam, and we oversee all steps — from design inspiration to finished product. We do not own our supply chain, which means there are no Ace & Tate factories, instead, we have longstanding partnerships with suppliers. We are proud to work with some of the most experienced and skilled factories in the industry. Did you know it takes over 60 manufacturing steps to make one pair of acetate frames? Let's get into it.
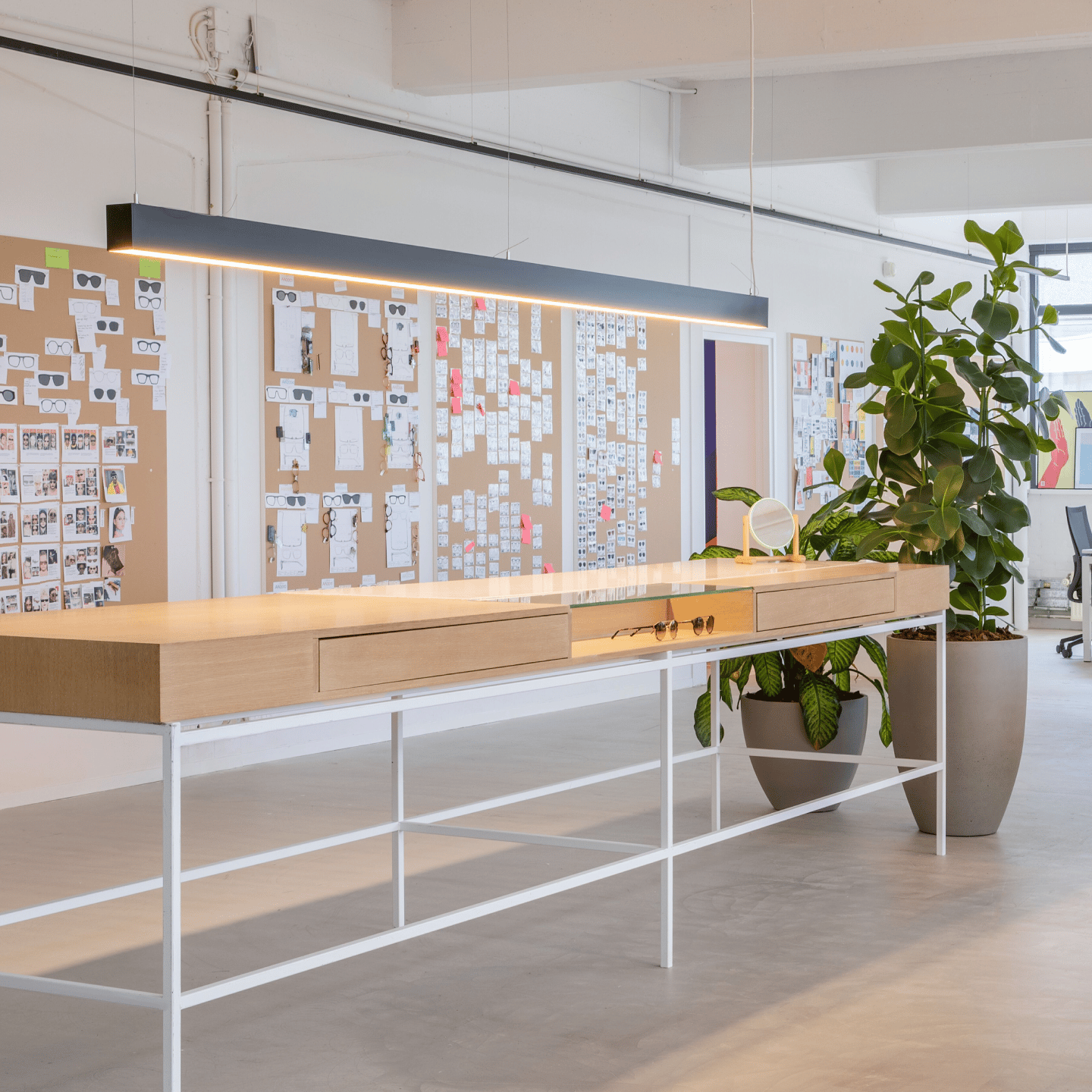
Designing the frames in-house
We’re proud to work with a dream team of in-house designers at our Amsterdam headquarters. They oversee the whole design process — from mood boards and material research, sketching from scratch, to fit and quality checks.
"Designing eyewear is unique; it's a meticulously considered product, because, it will be right there, on your face! I love the many restrictions the product challenges me with; size, weight, function, materials — it allows me to explore creativity within these limits. I aim to strike the right balance between form and function, wants and needs."
- Torunn Gullaksen, Head Designer
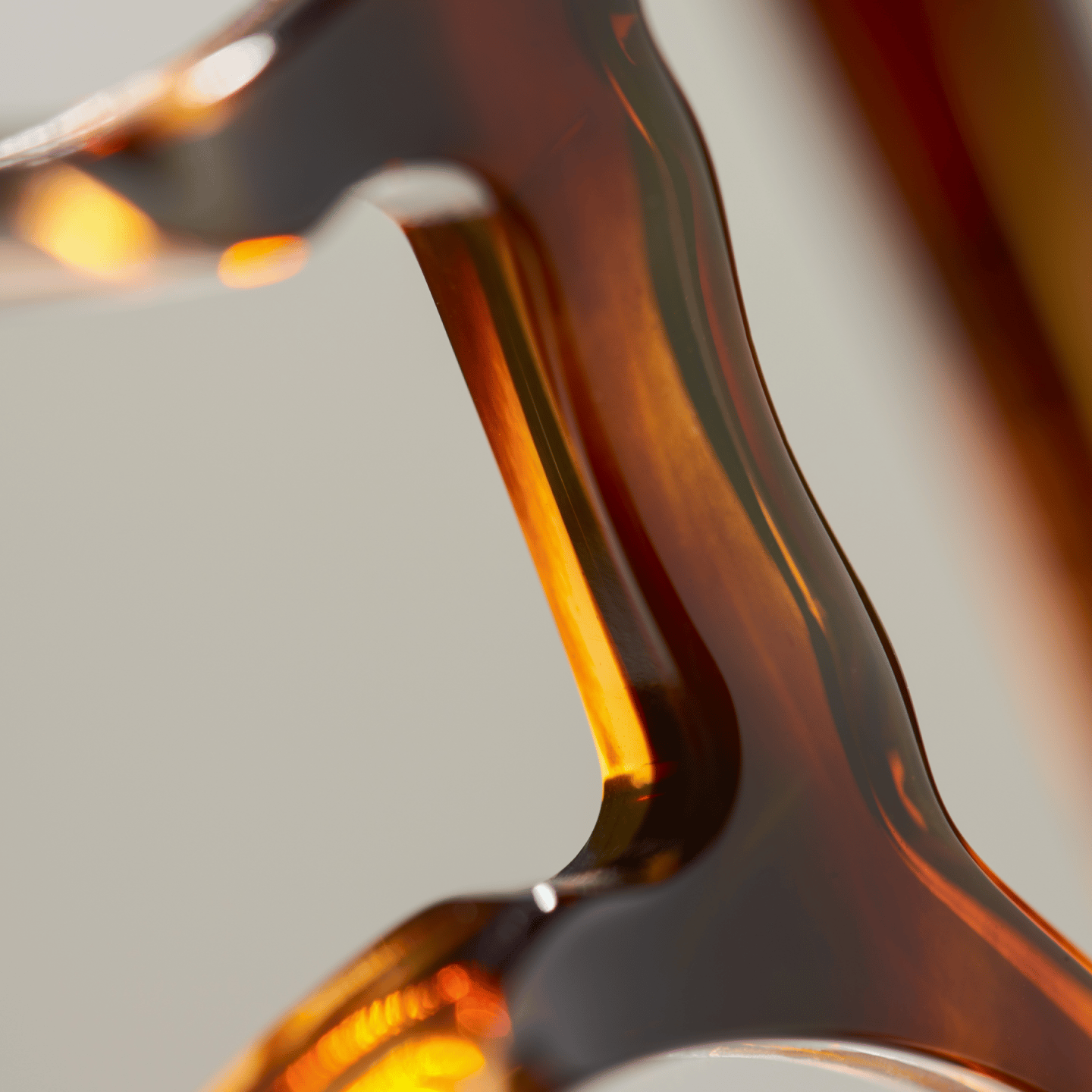
Sourcing the best materials
We have strict guidelines in place to source raw materials, lenses and other components. We aim to establish long-term partnerships with our business partners, based on consistency, quality, processes, impact (ethics and environment) and mutual core values. Our suppliers adhere to international standards and are required to sign our Code of Conduct.
We work with acetate manufacturers in China, strategically located near where our frames are produced. For our stainless steel and titanium frames, the raw material is directly delivered to the factory and finished in the requested colour at the factory.

Making the frames
Our frames are handmade by dedicated manufacturing partners following a long process — over one hundred steps that take three months. The combination of automated and manual steps make sure your frames get to you looking perfect.
We work with frame manufacturers in Vietnam, Cambodia and China: the best regions for eyewear production in the world. Choosing our manufacturing partners depends on the specific design and material requirements, allowing us the flexibility to select the ideal production location.
"At Ace & Tate, we collaborate with our suppliers to fully uphold our Code of Conduct. Together, we strive for continuous improvement, ensuring safe working conditions, respecting human rights, and supporting our suppliers in enhancing their social and environmental performance ."
- Ace & Tate Responsibility Team
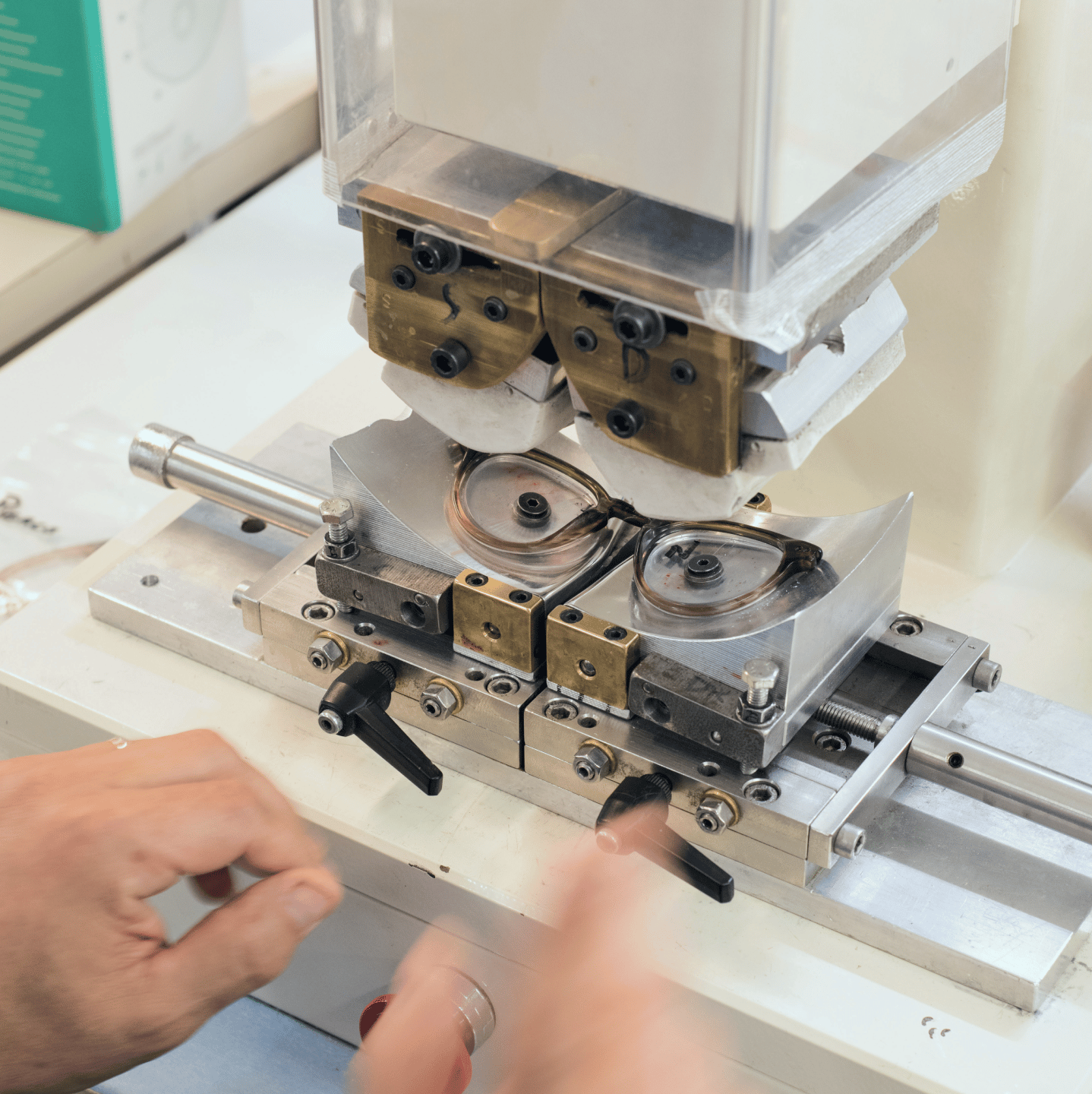
Mounting the lenses
We work with prescription lens suppliers in the Czech Republic and Thailand, as well as demo and sun lens suppliers in China. The lenses need to be edged and mounted onto the frames, this happens in Hungary or sometimes by our trained and skilled store staff in our stores.
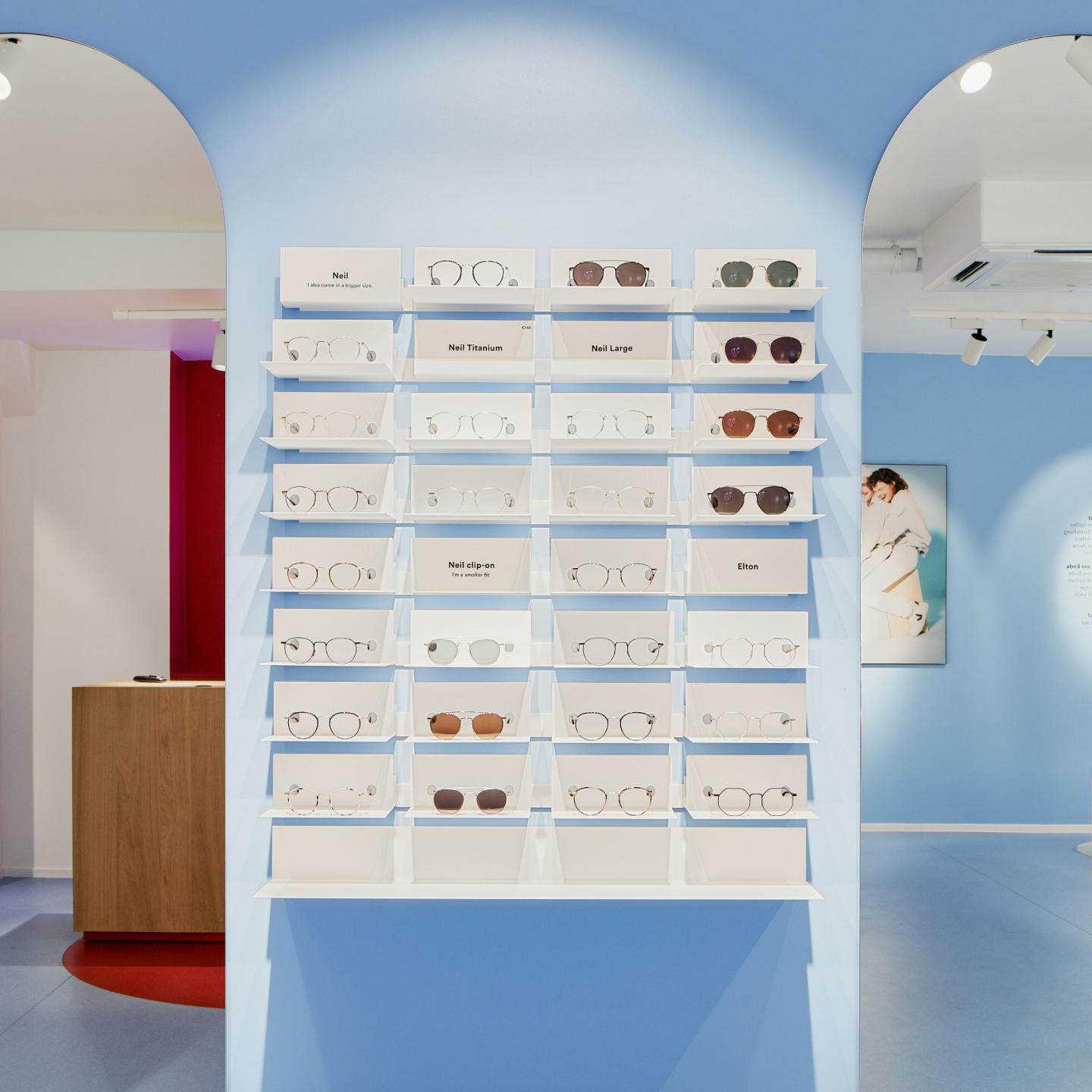
Packing up and sending off
Now that the glasses are completely assembled, it's time to ship them to our warehouses in the Netherlands and the UK. Here, the frames are prepared for distribution to either be sent directly to our physical stores or made available for online purchase.